DIY vs BUY - Soundproofing
Soundproofing and Acoustical Treatment Materials
Open cell foam sucks. And yes, that includes the so called premium open cell foam. (Sorry Auralex) Do not drop a ton of money on the foam based "total studio acoustical solutions". Is foam useless, no it is not. It however is only really effective on absorbing and reflecting very high frequency sounds. High frequency sounds dissipate quickly, are almost never the real problem with a rooms acoustics and can be controlled by a myriad of other materials that will also work to absorb and reflect more useful frequency spectrum ranges. Closed cell foam on the other hand can be useful as a building material, but it wont do enough on its own.
I do not have a local source for affordable premium soundproofing materials such as corning 703 or highend rockwool pannels, so all of the items that I used are available through most standard hardware stores. Due to the high cost of shipping these large heavy materials and the small size of my studio, it was actually more cost effective to purchase a few finished bass control products from smaller discount vendors which I will discuss later. If you have local access to these products or a larger studio, then do not hesitate to build using some of the good stuff. (I am still highly speculative of a few products like the $40 per bottle "acoustical adhessive" and fabrics that claim to have special acoustical properties) Are the items listed below the best options for soundproofing? No, they are not. They will do a good job on a budget though!
Materials Used On Projects
_
_ 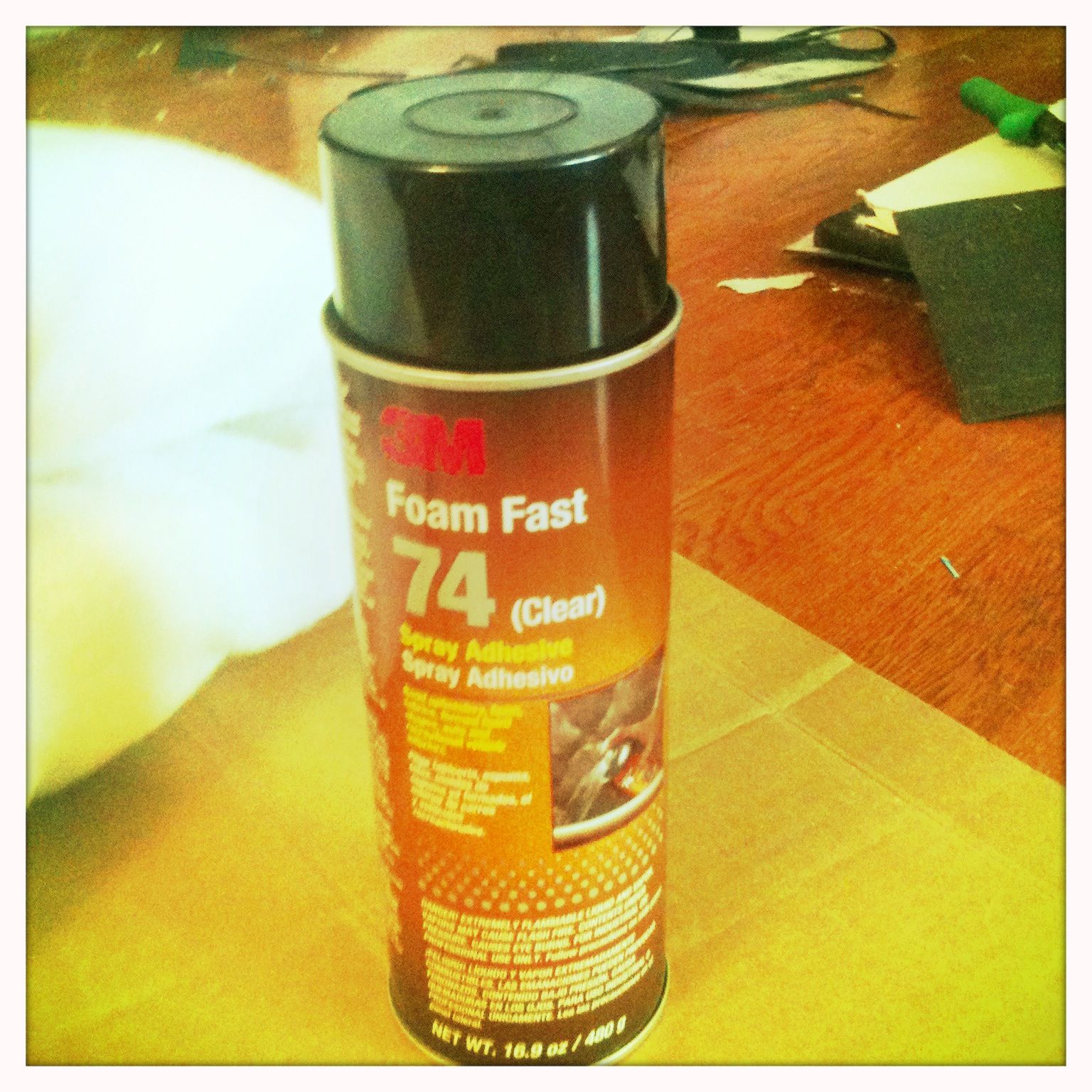
-2 rolls of Home Depot's dB-3 4 ft. x 8 ft. Acoustical Barrier. A relatively inexpensive dense roll of sheeting with decent sound reflection properties. (trimmed by heavy duty shears) ($29.99 per roll with free shipping)
-2 acoustic sound boards from Lowes 1/2" x 4' x 8' R1.2 Sound Board Acoustic Insulation (cut to specs by Lowes staff.)
-1 full size sheet of drywall (trimmed to size by box cutter.)
-1 heavy duty staple gun / staples
-6 bottles of Polyseamseal all purpose adhesive and caulk and caulk gun, or a similar adhesive that works with wood, foam, cloth, plastic and rubber.
-1" thick closed cell acoustical isolation foam (can be trimmed to size with box cutter)
-Linoleum flooring as an inexpensive sound reflection surface. (part of original super cheap window plug design)
-2" thick closed cell acoustical isolation foam - can be trimmed to size by box cutter and careful breaking. (part of original super cheap window plug design)
-1 roll of 6" thick backed fiberglass with long enough batts to handle the project.
-Thin plasic paint drop guard to cover the fiberglass for allergy and breathing irritation reasons. (2 mm is fine)
-Some inexpensive knit style cloth material to cover the fiberglass absorptive panel.
-Gorilla grip duct tape.
-Water based paint so that it won't dissolve the foam on the diffusers